Careful planning and design is crucial for ensuring that electrical maintenance work can be performed without the need for load interruptions. This allows some parts of an electrical distribution system to remain energized while maintenance is being performed, resulting in minimal disruption to the power supply and a reduction in downtime.
Effective engineering and design planning includes features such as modular design, which allows for easy replacement of components, and several different access points for inspection. This allows for the equipment to be maintained more easily and efficiently, reducing the need for load interruptions.
These special openings, which are typically located inside hinged doors, allow technicians to visually inspect the equipment without having to turn it off. With complete barriers, technicians can work safely on de-energized compartments while adjacent compartments are still energized, thus eliminating the need to shut down the entire equipment.
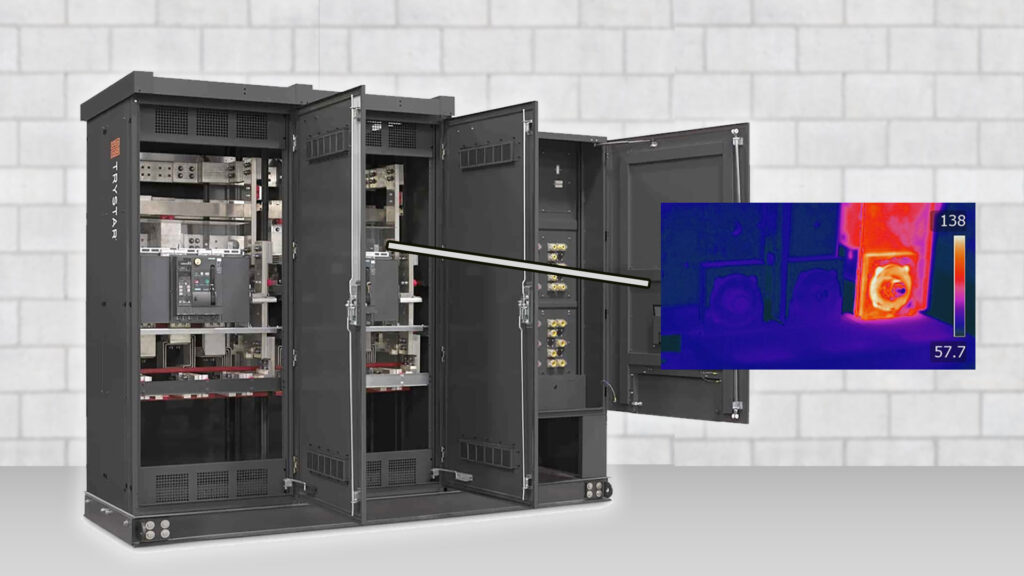
While these access points are useful for general inspection, an effective electrical preventive maintenance program requires equipment be de-energized periodically. There are several steps you can take to reduce the required downtime and make your electrical preventive maintenance program more efficient.
1. Keep everybody on the same page
Having a good understanding of the entire maintenance plan by all personnel involved is an essential step in the planning process. A kickoff meeting and task review helps everyone stay focused on the goal and provides an opportunity to discuss what to do in an emergency.
This is also the time to allow others to discuss any questions or concerns to everyone as a group. It is important that each person understands the role that others play to complete the task at hand.
2. Know your system
In any planning process, it’s crucial that all personnel involved have a thorough understanding of the entire power system. It is important to have a comprehensive understanding of the various loads connected to the system, including their unique service requirements.
To achieve this, it’s essential to provide maintenance technicians with easy access to diagrams, procedures, and safety precautions. Maintain a complete list of all the equipment associated with a given process to ensure that everything is maintained during one shut‐down.
These resources serve as helpful aids in keeping everyone informed and up-to-date, which ultimately ensures a safer and more efficient work environment.
3. Perform non-destructive tests prior to shutdown
Non-destructive testing is the act of taking measurements while electrical systems remain energized at power frequency to assess potential problems before they arise. Infrared cameras are ideal for inspecting electrical systems because they do not require contact and can be performed quickly with equipment in service.
Online Partial Discharge testing is a non-destructive, non-invasive predictive maintenance tool that gauges the condition of insulation systems based on measuring discharge at the system operating voltage. With suitable sensors, PD activity can be monitored and trended either on a temporary or continuous basis.
4. Prioritize Your Tasks
The main benefit of non-destructive testing is that it allows an asset owner to find problems that they may have not suspected and prioritize their maintenance plan, which is critical in order to minimize downtime and focus technical resources efficiently.
Comparisons can be made between similar components to make a relative assessment. This offers an excellent means of troubleshooting because an anomaly doesn’t need to be fully understood in order to determine whether further investigation is required.
Once the baseline is established, any equipment that deviates is given the most focus while systems are down.
5. Keep good help on hand
When unexpected issues arise with your electrical equipment, it’s important to have knowledge of the services available from electrical maintenance contractors that have specialized test equipment in your area.
These contractors have the necessary tools and technical expertise to handle any type of problems that may arise. They can help diagnose problems quickly and accurately, and provide solutions that minimize downtime and keep your equipment running smoothly.
Most reputable electrical testing contractors offer 24 hour emergency response. Having knowledge of these services in advance can save a lot of time and hassle when an unexpected problem occurs. It also can help you plan for maintenance and budget accordingly.
Maintaining a list of qualified electrical maintenance contractors in your area can provide peace of mind, knowing that you have a reliable resource for quick response and effective solutions should something go wrong.