The use of advanced robotic technology is rapidly making waves across the electric utility sector, taking on extreme tasks, conducting precise maintenance, and making hard-to-reach areas more easily accessible for service technicians. Broader developments in machine learning, automation, and digital imaging have turned once simple machines into extremely versatile tools for the power industry.
Inspection robots enable system operators to plan efficient outages more precisely, thereby reducing the downtime required to conduct maintenance tasks. This increases equipment reliability and increases the safety of people and the environment.
Drones / UAS
Inspection and maintenance of high voltage transmission lines is a dangerous job that involves climbing massive structures or traversing a thousand miles of high-voltage transmission lines via helicopter. The work is time-consuming, costly, and poses substantial risk to human life.
In an effort to avoid taking lines out of service, helicopter technicians with special equipment crawl over energized cable, hundreds of feet above ground. Voltage levels of 500kV pass over their bodies as they work, like a bird resting a power line.
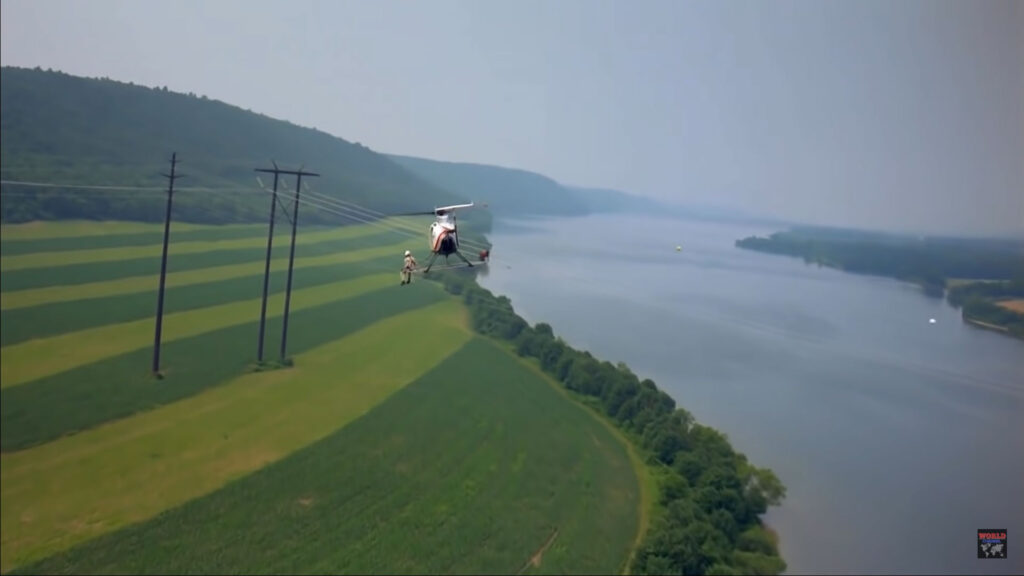
Advances in commercially available drone technology now allows humans to assume far less risk from the ground. Remote controlled aerial vehicles can easily be equipped with an array of sensors, making them ideal robots for troubleshooting and routine inspection of overhead electrical equipment.
Drones designed for maneuvering within confined spaces can be fitted with 3D cameras and laser based navigation for inspecting small areas such as an underground cable vaults. This allows for more articulate inspection from outside the space compared to traditional endoscopic camera methods.
Transmission Line Robots
Similar to how traditional technicians traverse a transmission line, small, autonomous crawler type robots connected to a line can conduct regular surveillance of cable and insulator condition. These devices can draw power directly from the line, perform work around the clock, and be controlled remotely. By pausing in one spot, the robots can capture better quality images than those taken from a helicopter flying at 30 to 60 miles per hour.
As part of a joint partnership, the Prysmian Group and Exelon Energy used a transmission line robot to apply a special coating to existing 138 kV overhead power lines, resulting in lower conductor operating temperatures and increased capacity. The Prysmian “E3X” coating increases emitted thermal radiation and reduces solar absorption, enabling lines to run cooler, reduce energy losses and avoid sag related safety issues.
In late 2021, the pilot successfully demonstrated the application via a robot on close to a mile of ACSR overhead lines managed by ComEd, an Exelon company that serves northern Illinois. This was a first in the industry for grid-enhancing technology.
“Ti” the Transmission Line Robot
The world’s first fully autonomous transmission line robot (named “Ti”) was developed by The Electric Power Research Institute (EPRI) starting in 2009. Ti glides along the shield wire above energized conductors, covering an average of 3 miles per day drawing energy from the transmission line’s electromagnetic fields at key points to charge its batteries.
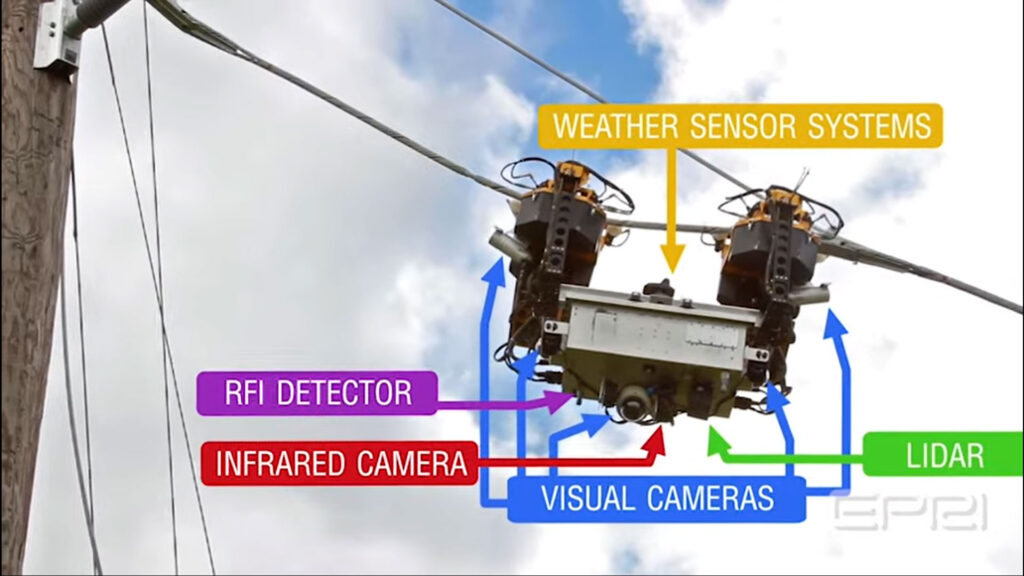
As the robot glides along the line, it takes photographs and collects various readings, transmitting them in real time back to maintenance crews. Ti’s high-definition visual and infrared cameras inspect rights-of-way and components and determine clearances between power lines and trees. Electromagnetic interference detectors can locate discharges such as arcing.
The robot was deployed in Ohio on a 75-mile segment of a 138-kilovolt transmission line operated by American Electric Power. Moving at speeds up to 5 miles per hour, the robot was able to complete its work within five weeks.
Some instruments that can be deployed with Ti include: lightning sensors, vibration sensors for windy areas, and leakage current sensors for coastal areas where salt can contaminate components.
Insulator Robots
Power line maintenance, especially in remote areas without adequate personnel, can be a challenging task. The need to mitigate safety risks posed by polymer insulators has led to advances in research on insulator robots.
The Substations program at EPRI is a leader in robotics research for the power distribution sector and has demonstrated potential uses for remote maintenance in the area of overhead transmission and ground level inspections.
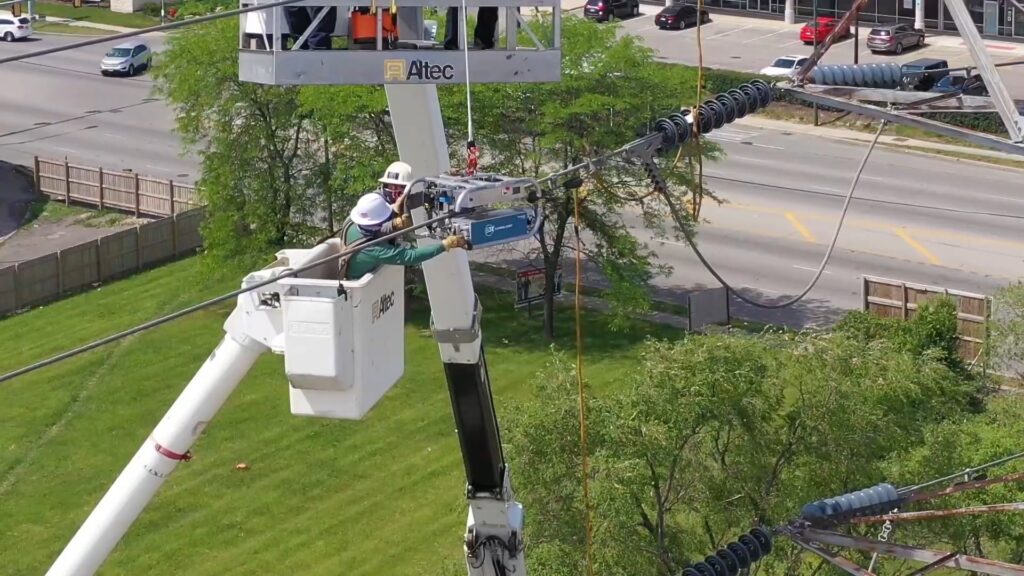
EPRI conceptualized a crawler robot fitted with a LiveLine Tool designed to take leakage current measurements on transmission line tower insulators, which can be 3 to 15 feet in length and suspended hundreds of feet above ground, depending on the transmission line voltage.
Maintenance crews send the robot to crawl up the insulator, it collects readings with the test equipment, and then crawls down back down to technicians who can analyze the results. The robot is also capable of knowing whether the unit is acceptable on its own.
When EPRI lab-tested the robot with 10 different insulator configurations, the measurements proved to be more consistent than those obtained by manual hotstick.
Internal Inspection Robots
Another type of crawler are small, low-profile units that are fitted with tiny lights and ultra high-definition cameras. These bots can move through confined and underground spaces, like manholes, to inspect cables and other equipment in tight places.
Crawlers are the most commonly deployed robot for generator inspections. They typically use “caterpillar” tracks (like those found on military tanks) to move through a narrow air gaps between the generator’s rotor and stator. QR codes serve as codes and reference points for the robot along the inspection route.
Various inspections and tests can be conducted within the generator using any combination of camera and sensors. The robots connect to a power supply and control hardware through cables and transmit data for processing.
As robot technology improves, thinner robots can be deployed to access more generators with smaller air gaps.
Substation Grounds Robot
Autonomous wheeled or tracked robots that use cameras, infrared, sound, and motion sensors are becoming more widespread to conduct ground level equipment inspections and bolster security in electrical substations.
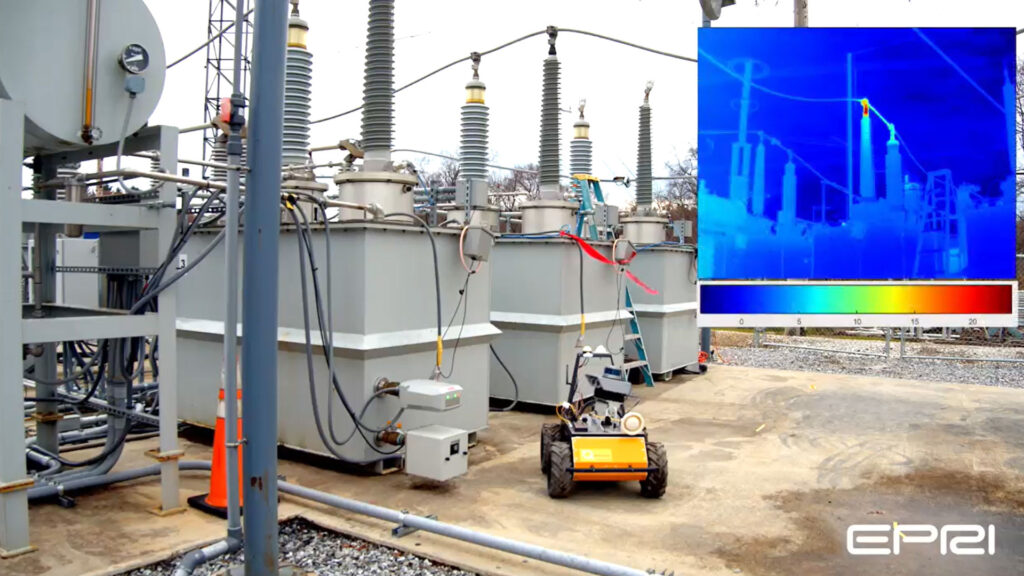
Inspection robots don’t need technicians to control them as they are capable of conducting visual, infrared and corona inspections all on their own. When something unusual is spotted, the robot reports back to a diagnostic center for review and correction before customers are ever affected.
Florida Power and Light developed its own autonomous robot to perform outdoor substation infrared inspections. The robot is programmed to conduct two inspections per day and can be controlled on demand via remote operation.
Shortly after implementation, the robot was able to successfully identify equipment that was overheating and alerting crews who responded to fix the issue. The utility estimates the device saved nearly 10,000 customers from potential power loss.
Boston Dynamics “Spot”
Spot is an agile mobile robot developed by Boston Dynamics that resembles a pet dog and can navigate terrain with unprecedented mobility. It embodies the latest advancements in robotics, allowing its users to remotely control and automate inspection procedures.
In 2021, Duke Energy purchased Spot to perform inspections in hard-to-access areas at the Oconee Nuclear Power Station. Equipped with a camera and audio controls, the four-legged friend is led remotely by technicians, allowing them to operate more safely while robotics assume the risk.
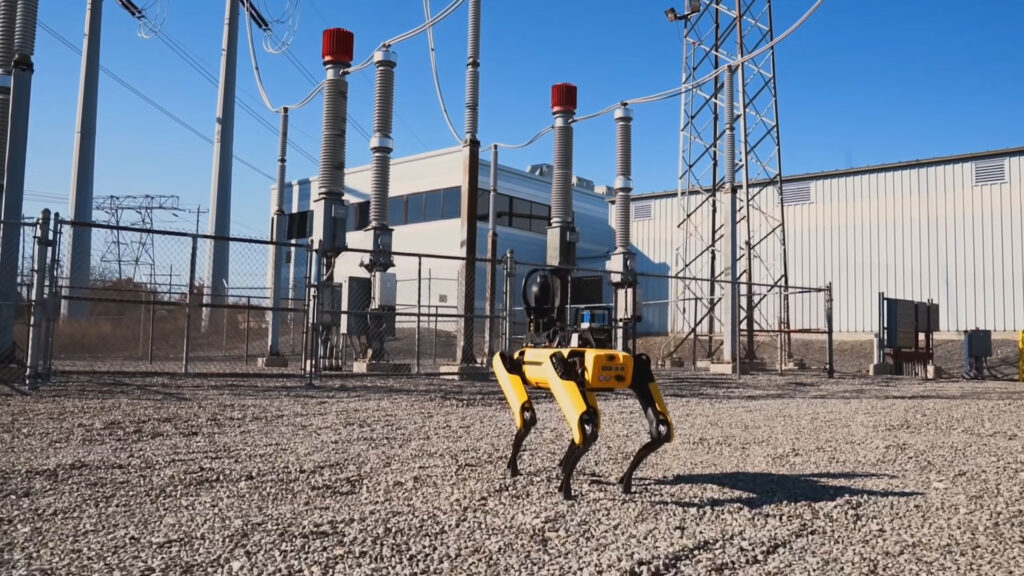
Inspection robots like the ones being implemented by Duke Energy are being equipped with more advanced diagnostic tools and machine learning capabilities that would allow it to perform routine inspections without controller manipulation.
The use of artificial intelligence (AI) with robotic inspections can further enhance results, allowing autonomous robots to determine acceptable and non-acceptable conditions. The company is also experimenting with articulating arms that could potentially be used to manipulate controls.
Energy giant National Grid introduced Spot to their Sandy Pond Converter Station in 2021, just a few days before a planned shutdown period. The inspection robot was equipped with both a high-resolution 30X optical zoom pan/tilt/zoom camera and IR camera to detect signs of potential problems.
Robotic technologies like those offered by Boston Dynamics are a great choice to bolster security within substation grounds alongside traditional motion sensors, lights, etc. These type of robot are very agile, move quickly, and can be fitted with infrared, night vision, and a variety of deterrent systems.
Challenges
While the future of robotics and autonomous inspections looks promising, research and development in the robotic inspection space is faced with several challenges. For example, in the case of using crawlers, not all generator air gaps can be accessed and some equipment requires precise maneuverability that not all robots can provide.
Robotic inspections also require technicians to interpret camera images, which sometimes distort color and size. Although distortion can be corrected and enhanced using AI, traditional visual inspections enable humans to view defects directly at close range.
As with any mobile technology, robots have batteries that have limited run time and need to be exchanged. Most batteries are rechargeable, but reliable charging technology has not yet been able to demand.
References
- Robots Take on Tough Tasks in Transmission and Distribution
- Robotic substation inspection technologies
- Smart overhead powerline robot, clever innovation
- Adding Value to Power Distribution: Autonomous Inspections at E.DIS