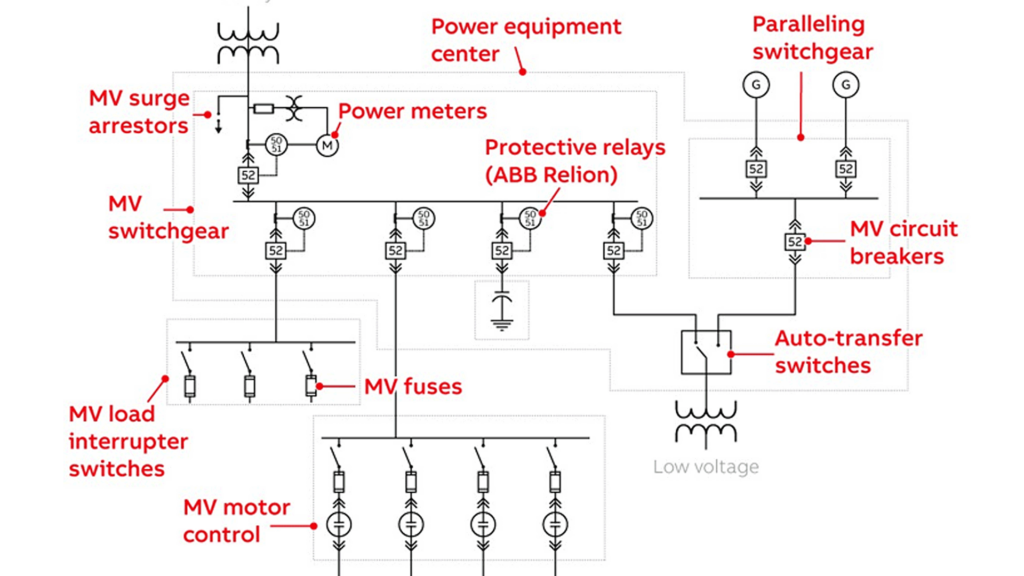
With the release of the 2023 edition, NFPA 70B became an enforceable standard by introducing mandatory language for the maintenance of electrical equipment. Prior versions were labeled as a “recommended practice” for electrical maintenance.
Facility managers are now required to create and carry out an effective electrical maintenance plan, but it can be an overwhelming task without the proper guidance. In this article, we will try to shed some light on effective maintenance practices and how you can get started right now with creating a plan for your facility.
Understanding the 3 Main Approaches to Electrical Maintenance
All electrical equipment requires routine maintenance to ensure the continuous delivery of reliable power. Typical maintenance plans for electrical power apparatus are developed based on estimates, calculations, and manufacturer’s literature. There are three primary approaches to implementing an electrical maintenance program:
- Time Based Maintenance (TBM) – Derived from manufacturers estimates and calculations. Often subjective, expensive and prone to technical and human error. Can result in minimal benefit for maximum effort.
- Condition Based Maintenance (CBM) – Relies on periodic testing such as an annual maintenance outage. Production systems are shut down and electrical equipment is de-energized. Destructive testing methods are used. Work must be completed within a time constrained window. Highly prone to human error and failure upon re-energization.
- Predictive Based Maintenance (PBM) – Advanced maintenance practices that utilize non-destructive testing technology such as sensors (light, sound, gas, radio), computer analysis, and machine learning to monitor and pinpoint anomalies with the system in service. Methods can be deployed on nearly any frequency that suits the asset owner or they can be installed permanently as part of a 24/7 condition based monitoring system.
A comprehensive maintenance program considers industry standards, clear procedures, documentation, training, and regular evaluation. By balancing these approaches, organizations can optimize performance, reliability, and safety of their electrical power systems.
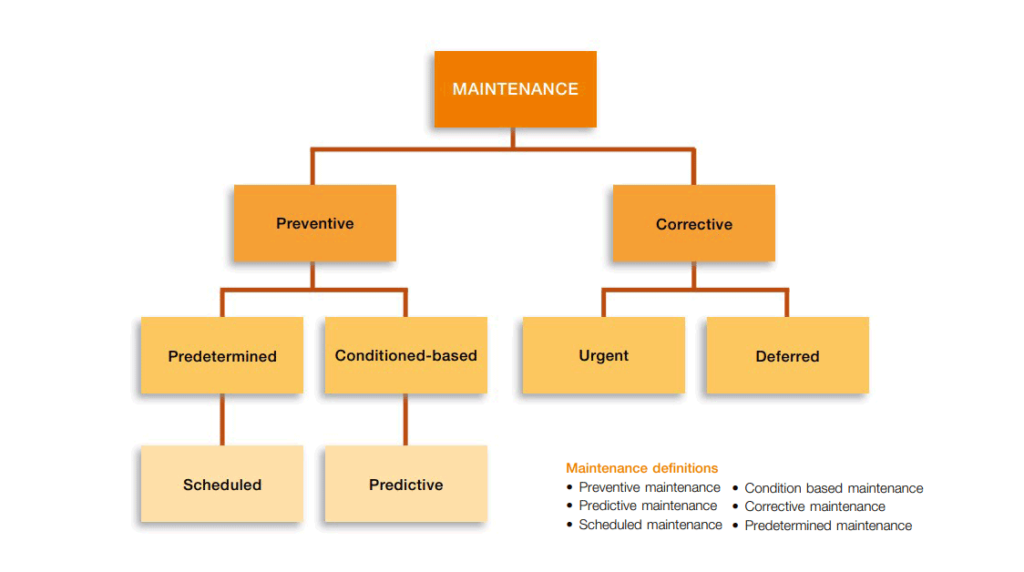
Creating a Maintenance Plan, 7 Key Points to Follow
Whether you’re managing a commercial facility, an industrial plant, or entire substation, understanding the key principles of electrical maintenance can help you avoid unexpected outages and costly repairs.
1. Evaluate the System, Inventory Assets
The first step in any comprehensive electrical maintenance program is gathering an inventory of the equipment in your system. This will include the entire distribution system, from the utility to main distribution panels and beyond. Group the equipment by voltage class (medium-voltage and low-voltage) and then by type (switches, transformers, switchgear, circuit breakers, panels, batteries, etc).
2. Determine Reliability Requirements
Evaluate your equipment inventory list and highlight the equipment that is most critical to your mission. This will be the equipment that receives the most attention, as maintenance windows have tight time constraints. It may not be possible to complete everything, so it’s important to prioritize which equipment gets addressed first. You may need to schedule several outages throughout the year to maintain the entire system.
3. Evaluate Asset Condition
The condition of your equipment will determine how much maintenance attention it needs. Conduct a walk-through of your equipment and perform a visual inspection from a safe distance. Evaluate the operating environment and prioritize assets that are in the worst condition but have the highest reliability requirements.
4. Consult Industry Standards
Having a strict maintenance regimen is the best defense against electrical failures. Consult NETA MTS “Frequency of Maintenance Tests” (Appendix B) to determine how often you should perform inspections and tests based on the criticality and condition determined in the previous steps. This matrix will help you determine how often each piece of equipment needs to be tested and which tests to perform.
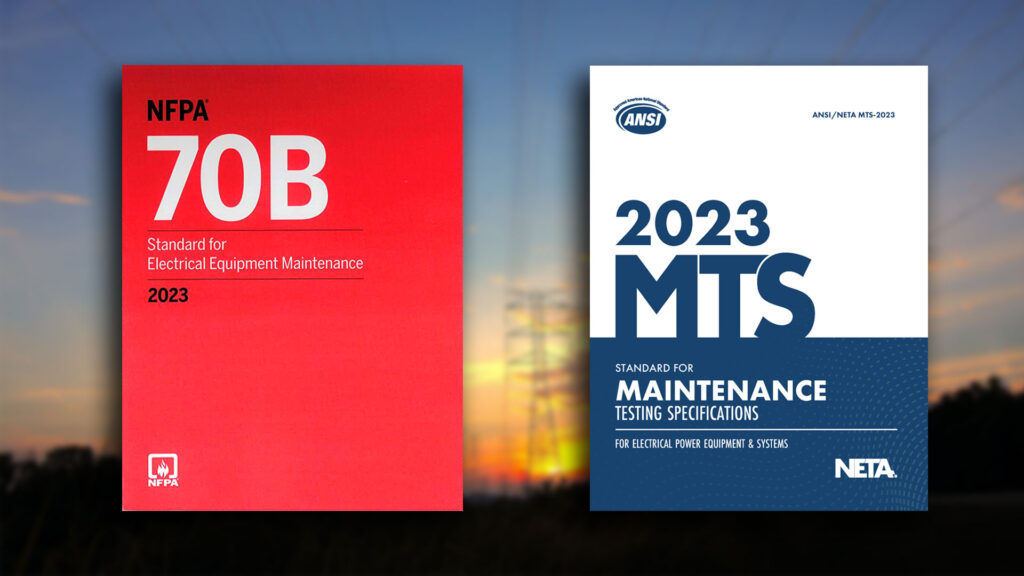
5. Collect Baseline Readings
If you don’t have any prior maintenance records on hand, it’s important to collect baseline readings to compare with future results. This will typically be in the form of factory and third-party acceptance test records, so obtain as much history as you can. If this information is not available, your first maintenance outage will serve as a baseline for the future.
6. Perform an Infrared Scan Prior to Your Maintenance Outage
Thermography inspections have consistently been proven effective in identifying various hazardous situations and potential failures in electrical distribution systems. To proactively approach electrical maintenance, it is cost-effective to use a high-resolution infrared camera to regularly scan critical parts of the system.
Infrared cameras are ideal for inspecting electrical systems because they do not require contact and can be performed quickly with equipment in service. Conducting an infrared scan prior to the maintenance outage can pinpoint areas of concern that take priority when the power is off.
7. Follow Up and Trend per Industry Standards
It’s important to stay disciplined in your electrical maintenance plan to maximize its value. Maintain thorough test records and compare your readings with previous maintenance schedules and industry standards. Ensure you use temperature-corrected values and track your data over time to predict failures before they become major issues.
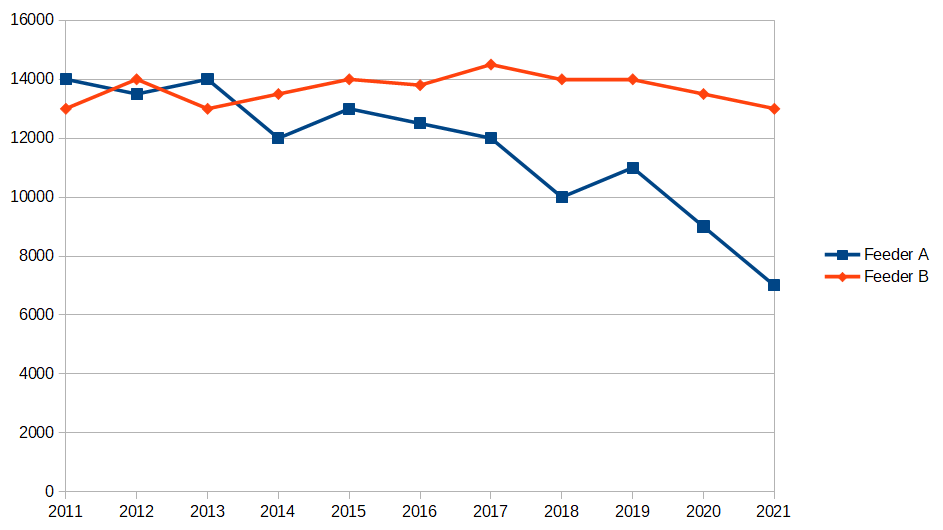
Enhancing Reliability through Effective Maintenance Strategies
Routine maintenance is the key to a reliable power supply in all electrical equipment. To achieve this, comprehensive maintenance plans for electrical power apparatus are created based on estimates, calculations, and manufacturer’s literature. These plans help ensure that the equipment operates efficiently and effectively, minimizing the risk of unexpected failures or disruptions.
Furthermore, regular maintenance allows for the implementation of necessary repairs, upgrades, and improvements, ultimately enhancing the overall reliability of the electrical power system. By adhering to these maintenance schedules, organizations can proactively identify and address potential issues, thereby extending the lifespan of the equipment and optimizing its performance.