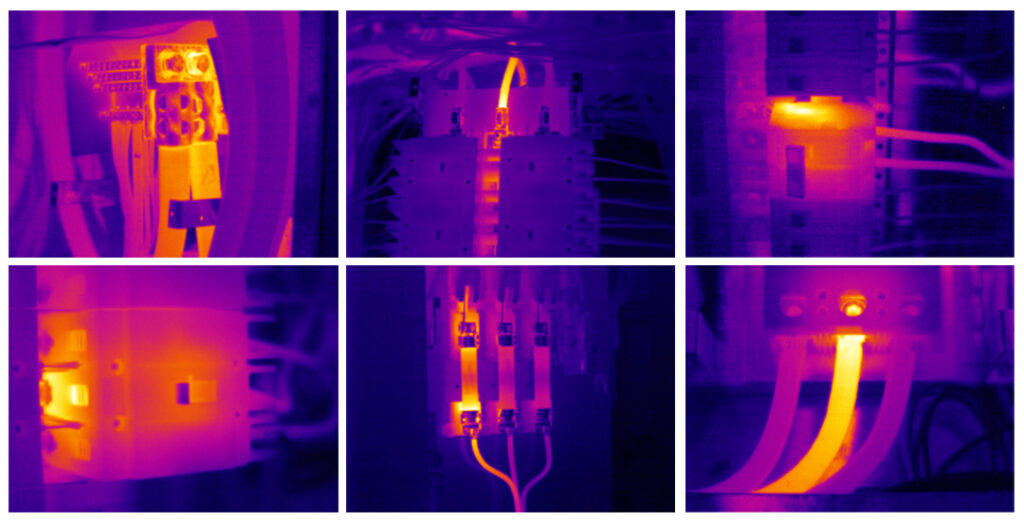
An electrical distribution system consists of numerous connection points that should be regularly inspected to avoid serious problems like overheating and high resistance, which can lead to catastrophic failures. To take a proactive approach to electrical maintenance, it is cost-effective to use a high-resolution infrared camera to scan critical parts of the system on a regular basis.
Thermography inspections have continuously been proven effective in identifying various hazardous situations in electrical distribution systems. By diagnosing issues accurately and taking prompt corrective action, significant losses due to equipment damage and company downtime can be prevented.
The National Fire Protection Association’s (NFPA) 2023 edition of 70B now requires electricians to use thermal imaging to verify temperature differentials on equipment they inspect. In this article, we will provide some insight about infrared (IR) scanning by addressing several commonly asked questions.
1. Should you hire a contractor for IR Scans or do it in-house?
Infrared surveys can be accomplished either by in-house maintenance teams or by a qualified outside contractor. The associated costs, safety risks, and effectiveness should be carefully weighed by facility managers to choose the best approach.
Many organizations find it preferable to hire an outside contractor rather than invest in expensive scanning equipment and the required training for their personnel. Because outside contractors have more extensive experience, their findings and recommendations are likely to be more accurate, practical, and economical than those of a part-time in-house team.
Hiring a qualified contractor to guide you in the process of planning and training your in-house staff can help reduce costs over the long term if your facility requires frequent infrared inspections on a large scale. In this case, a qualified contractor can be brought in to provide root cause analysis and expert repair services when problems are found by in-house staff.
Unless the amount of infrared work is sufficient to keep maintenance personnel active throughout the year, the use of specialized contractors should be considered.
2. What makes a qualified thermographer?
Asking a contractor to maintain or test a piece of equipment usually creates a false sense of security that can be shattered by a serious failure caused by inadequate service or incorrect maintenance procedures. The result is often the same when supervisors do not provide the necessary training to their in-house personnel.
One of the main factors that can limit the effectiveness of thermography is the skill and knowledge of the thermographer performing the work. The thermographer plays the most important role in thermography, and their expertise is crucial.
Merely knowing how to operate a camera and produce IR images is not sufficient for a thermographer. While thermal imagers have their limitations, infrared technicians can overcome them by selecting appropriate equipment and utilizing correct inspection techniques.
A professional thermographer must possess a strong understanding of infrared theory and heat transfer principles. They should also be aware of how site conditions and weather can affect the accuracy of their results. At the very least, a thermographer should have a basic understanding of how the equipment they are inspecting functions.
When a thermographer is unfamiliar with the components they need to inspect, it is their responsibility to acquire the necessary knowledge to conduct the infrared inspection properly. A thermographer must always strive to be an expert in their field and be honest about recognizing their own limitations. Anything less than that compromises the final results of a project even before the inspection begins.
3. Does infrared scanning replace visual inspections for electrical maintenance?
Infrared surveys should never be viewed as replacement for visual inspections of electrical systems but rather a complementary task. Visual inspections or checks are still required on lightly loaded circuits, or circuits not energized or not carrying current at the time of the infrared survey.
External conditions that provide evidence of heat damage include:
- Discoloration, usually a darkening, of materials or finishes
- Crazing, cracking, and flaking of varnish coatings
- Embrittlement of tapes and cable insulation
- Delamination of materials or finishes
- Generalized carbonization of materials or finishes
- Melting, oozing, or exuding of substances from within an insulating assembly
4. What is the main advantage of infrared scanning?
Using infrared detection is a reliable and efficient method in a variety of electrical systems. Thermography is most effective in situations where it’s not possible to shut down equipment or when mission critical operations would be impacted.
Infrared inspections are valuable for assessing past repair work, verifying the integrity of new electrical installations, and examining equipment that is still covered by warranty. Conducting IR scans can be a cost-effective approach, especially when considering the potential savings from preventing equipment damage and business disruptions.
Implementing regular infrared inspections may involve adjusting electrical maintenance priorities and monitoring equipment performance trends over time. This proactive approach helps identify issues that require periodic observation and ensures ongoing operational efficiency.
5. What are the disadvantages associated with thermographic inspections?
Certain types of infrared equipment have their individual drawbacks when it comes to ownership. Scanning-type thermal imaging devices, for instance, can be expensive to purchase outright. Additionally, operating such instruments requires training and certification, which can be an expensive investment.
Infrared inspections demand special considerations and analysis. Enclosed equipment, designed for safety or reliability, can present challenges in terms of scanning or detecting thermal radiation from within. Satisfactory measurements may require the removal of panel covers, which can pose risks to both the facility and inspection personnel.
Weather conditions can also affect surveys of outdoor electrical systems, such as overhead power lines and substations. Rain and wind can cause abnormal cooling of faulty conductors and components.
When working on outdoor equipment, the reflection of sunlight on bright surfaces can be misinterpreted as hot spots. Therefore, infrared work on such equipment might need to be carried out during nighttime.
However, this presents another problem because electrical loads are typically lower at night, and faulty connections or equipment may not generate enough heat for detection. Reflective surfaces, which do not efficiently emit radiation energy, can appear cool in the infrared image despite being hot (referred to as “low emissivity”).
6. How often should you perform IR Scans?
Regular infrared inspections of energized electrical systems should ideally be conducted on an annual basis before planned shutdowns. This approach helps focus maintenance efforts on any issues found and allows for re-scanning once the equipment is back online to verify the effectiveness of repairs.
In cases where loss experience, installation of new electrical equipment, or changes in environmental, operational, or load conditions warrant it, more frequent infrared inspections should be performed, such as quarterly or semiannually.
During the infrared inspection, its important to include all critical electrical equipment as determined by the facility (refer to NFPA 70B). Special consideration should be given to utilization equipment that serves equipment operating for extended periods between shutdowns.
Equipment, whether electrical or otherwise, should be deemed critical if its failure to operate normally and under full control poses a serious threat to people, property, or production. Making this determination might require the combined knowledge and experience of multiple individuals.
In a small facility, the facility engineer or lead mechanic, in collaboration with the operating superintendent, should be capable of making this determination.
7. How much system load is required for effective IR scans?
Infrared surveys should be performed during periods of maximum possible loading but not less than 40 percent of rated load of the electrical equipment being inspected per ANSI/NETA and NFPA 70B standards. The circuit-loading characteristics should be included as part of the documentation provided to the facility.
8. How accessible must the equipment be for an effective inspection?
Whenever feasible, equipment enclosures should be opened to provide a direct view of components during infrared inspections. However, in certain cases, such as with busway systems, it may not be practical to open the enclosure. It’s important to note that internal temperatures in such cases can be higher than surface temperatures.
Additionally, it’s worth mentioning in the inspection report that plastic and glass covers used in electrical enclosures are not transparent to infrared radiation. Skilled thermographers can either overcome these limitations or highlight them to their clients, ensuring they are aware of any potential impact on the accuracy of the inspection.
9. What happens when a problem is found during an IR inspection?
The electrical supervisor should be immediately notified of critical, impending faults so that corrective action can be taken before a failure occurs. Priorities should be established to correct other deficiencies.
ANSI/NETA MTS, Standard for Maintenance Testing Specifications for Electrical Power Distribution Equipment and Systems suggest temperature benchmarks similar to those in the following list:
- Temperature differences of 1°C to 3°C indicate possible deficiency and warrant investigation.
- Temperature differences of 4°C to 15°C indicate deficiency; repairs should be made as time permits.
- Temperature differences of 16°C and above indicate major deficiency; repairs should be made immediately.
Its important to note that the temperature differences in the above list denote differences from the normal referenced temperature. The normal referenced temperature is determined by a qualified technician.
10. Special considerations for equipment reliability
Depending on the size and criticality of your power system, it is beneficial to prioritize maintenance investments in areas where equipment plays a crucial role in facility production. Below is a list of common items that should receive special attention:
Electrical Conductors
All exposed conductors should be visually inspected for evidence of overheating at bolted joints. Extreme overheating can discolor copper conductors, deteriorate the insulation, and could require additional maintenance.
Fuses
Fuse terminals and fuseclips should be examined for hot spots and discoloration caused by poor contact or corrosion. Fuses are most commonly found in disconnect switches and control circuits.
Busway
Infrared inspection of busway joints can reveal loose connections and abnormal heating.
Transformers
The tank, heat exchanger, cooling fins, tubes, radiators, no-load tap changer, and all gasketed or other openings should be inspected for leaks, deposits of dirt, or corrosion. Infrared inspection can be used to detect fluid levels as well as flow restrictions in cooling tubes.
Electronic Equipment
Overheating as indicated by discoloration or other visual characteristics. Infrared inspection can reveal abnormal temperatures and possible problem areas.
UPS Systems
An infrared scan of batteries and UPS equipment should be performed. The scan should look specifically at the battery connections with ac input power disconnected and the battery supplying power to the load. The unit should not be operated under load for long periods of time with covers removed, because cooling might be inhibited, and the unit may become damaged.
Battery Banks
Batteries serving UPS systems and other critical equipment should be examined under full load with an infrared scanning device whenever a performance test is conducted. Infrared scanning can reveal problems such as abnormal temperature of a cell, a poor connection at a battery post, and a deteriorated link, strap, or conductor.
Terminal post connections should only be tightened when the need is indicated by resistance readings or infrared scan. Because the posts are usually made of lead, frequent tightening can degrade and permanently damage the posts.
Infrared: Your Secret Weapon against Electrical Failures
Thermography inspections offer valuable insights into the condition and performance of electrical systems. By utilizing infrared technology, potential issues can be detected, allowing for proactive maintenance and minimizing the risk of equipment failures, production disruptions, and safety hazards.
While there are some disadvantages associated with owning and operating infrared equipment, the benefits outweigh the challenges. Regular inspections, conducted at appropriate intervals, enable focused maintenance efforts, verification of repairs, and identification of emerging trends.
It is crucial to prioritize critical equipment and areas where facility production is paramount, ensuring that maintenance investments are directed where they are most needed. By adopting a proactive approach to infrared inspections and maintenance, businesses can improve operational efficiency, mitigate risks, and promote a safe and reliable electrical infrastructure.